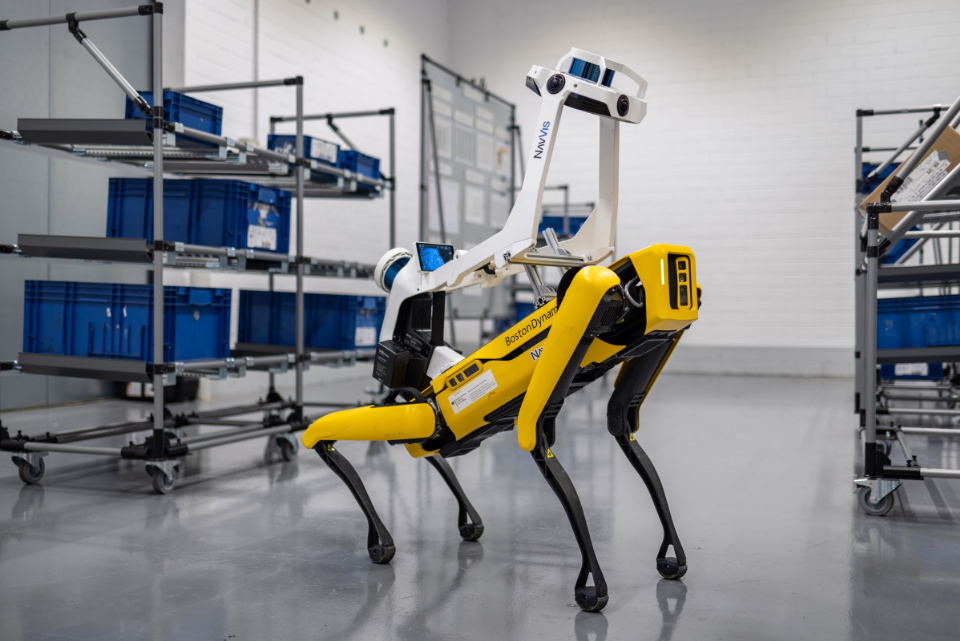
- モジュラーアセンブリにより、製品の柔軟性が高まり、作業が簡素化
- 車両表面のバーチャル検査が、設計、技術開発、生産におけるデジタルインターフェースとして機能
- ロボット犬Spot、生産ホールの3Dスキャンをサポート
- VRにより仮想世界でグローバルにネットワーク化された生産計画を実現
(ドイツ本国発表資料)
2022年7月26日、インゴルシュタット/ネッカーズルム:アウディは完全にネットワーク化され、極めて効率的で持続可能な生産を確立しています。その目標は、将来の課題に適切に対応できるように、機敏で柔軟なバリューチェーンを設計することです。これらには、モデルバリエーションの多様化、電気自動車への移行、不安定さを増している供給状況、政治的不確実性が含まれます。生産およびロジスティクス担当取締役 ガード ウォーカーは次のように述べています。「私たちは相乗効果を活用して、作業者から完全に自動化されたサイクルに至るまで、生産全体を見渡しており、オープンイノベーション文化の枠組みの中で、デジタル化を推進しています。私たちは効率的な価値創造を実現し、リソースと能力を柔軟かつ効率的に利用できるようにします」
モジュラーアセンブリには、組立ラインでの生産に比べてどのような利点がありますか?
組立ラインは、1世紀以上にわたって自動車生産の基本となってきました。しかし、現在ではその限界に近づいています。数多くの派生モデルと顧客の嗜好に基づくオプションにより、製品はますます多様化しています。そのため、従来のプロセスでは、その複雑な生産工程に対応することが困難になってきています。「モジュラーアセンブリは、将来の課題に対する私たちの回答の1つです」とガード ウォーカーは述べており、「私たちは、より柔軟で効率的な組み立てプロセスを実現しながら、特に従業員のためにデジタルテクノロジーを活用しています」と語りました。Audi Production Lab(アウディ プロダクションラボ)では、プロジェクトマネージャー ウォルフガング カーンのチームが、大量生産用のモジュラーアセンブリの準備に取り組んでいます。
アウディは当初、インゴルシュタット工場の車内ドアパネルの事前組み立てに、このコンセプトを導入しました。試験的なオペレーションでは、同一の組み立て手順に従うことなく作業が実施され、その代わりに各モデル固有のニーズが満たされます。AGV(無人搬送車)は、コンポーネントが組み立てられる工程にドアパネルを直接運びます。「価値創造とセルフガイダンスのコンセプトを採用することで、状況により、生産性を最大20%向上させることができます」とカーンは説明しています。さらに、モジュラーアセンブリを特定の製造ステップにリンクすることができます。例えば、現在では、1人の作業者がサンブラインドを取り付けることが可能になっています。これまで、この作業は、組立ラインで事前に設定された時間内に取り付けを完了しなければならなかったため、2〜3人の作業者を必要としていました。柔軟なシステムのもう1つの大きな利点は、身体的な障害のためにラインで作業できなくなった人々を雇用することができることです。一連の試験的オペレーション工程では、貴重な洞察が生み出され、エンジニアが様々な工程の組み合わせを導き出すことが可能になっています。プロジェクトマネージャー カーンと彼のチームの次のステップは、大規模なモジュラーアセンブリを、プレアセンブリに統合することです。
生産に関して、アウディはどのようにバーチャルテクノロジーを使用し、設計と開発プロセスにどのような影響を与えていますか?
モデルの様々なデザインや装備のバリエーションは、バーチャルテクノロジーを使用して、様々な環境や照明条件下で、迅速かつ効率的に確認することができます。喫緊の課題の1つは、可能な限り少ない試作数で、設計を生産に移行し、お客様のために市場導入することです。そのために、専門家はモデルの初期開発段階からツールの導入に至るまで、設計図を調査して、それらを量産段階で再現できるかどうかを確認します。車両表面の最終承認は、データコントロールマイルストーンと呼ばれるシステムで実施します。
そのための最も重要なツールは、パワーウォールと呼ばれる大画面です。これにより、車両をオリジナルのサイズで再現することができます。視覚化クラスター(合計26,000個のCPUを搭載したコンピュータークラスター)と組み合わせることで、車両をリアルに表現し、実際の光や影、反射の影響を計算して表示することができます。そのプロセスは、バーチャルテクノロジーを使用した、意思決定プロセスの基礎となっています。パワーウォールによる視覚化に加えて、アウディはヘッドマウントディスプレイを以前よりも多用しています。この方法の主な利点は、専門家がお客様の視点からバーチャルモデルを体験できることです。この特別なバーチャルリアリティシステムは、標準的なハードウェアとソフトウェアで実行できるため、迅速かつ柔軟にインストールすることができます。つまり、多くの人々が利用可能で、世界中のどこでも簡単に再現できることを意味しています。
このテクノロジーは、公差管理でも使用されます。このようにして、アウディは構造的および質的な観点の両方から、それぞれの仕様に合わせて特定のモデルを構築することができます。ボディの3Dシミュレーションを使用すると、コンポーネントとアセンブリの公差の影響を、車両の画像で予測することが可能です。シミュレーション結果は、バーチャルリアリティを使用して現実的に視覚化されます。それにより、アウディ生産部門の専門家は、時間と場所に関係なく、ほとんど追加のコストを発生させることなく、生産施設から初めて設計と開発プロセスに影響を与えることができるようになりました。
スマートプロダクションにおけるバーチャルアセンブリ計画の利点とは?
バーチャルアセンブリ計画は、素材のリソースを節約するだけでなく、様々な場所で革新的かつ柔軟な協力関係の構築を可能にします。これにより、計画プロセスでプロトタイプを作成する必要がなくなります。スキャンプロセスは、生産工程で使用するマシンとインフラを仮想的に配置するために使用できる3次元点群を生成します。このソフトウェアは、人工知能と機械学習に基づいており、アウディの従業員は、仮想的に組立ラインを構築することが可能になります。フォルクスワーゲンのIndustrial Cloud(インダストリアルクラウド)は、例えば、作業の場所を比較検討したり、他の生産ラインの適切なソリューションを計画に使用したりできる効率的なツールを提供しています。
現在、アウディはNavVisと協力して、Spotと呼ばれるロボット犬を試験運用して、3Dスキャンを可能な限り効率的に実行できるようにしています。2017年に生産拠点のデジタル化が開始されて以来、13の工場、約400万m2がその対象となりました。10万m2の広さ(例えば、ネッカーズルムのAudi A6の生産施設)をスキャンするには、一交代制で約3週間かかります。またスキャンは、夜間または週末にしか実施することができません。さらに、階段やドアなどの構造上の障害物により、スキャン作業がより困難になります。
一方ロボット犬 Spotは、自動的にスキャンルートを把握して、48時間でスキャンを完了することができます。アウディは2021年12月以来、集中的にSpotをテストしています。プロジェクトマネージャー アンドレ ボンガルツは、次のようにコメントしています。「テスト結果は非常に有望であり、定期的に更新することができます。入力データは絶えず入ってくるので、新しいクルマの計画に使用できます」。アンドレス コーラーのチームが担当するバーチャル画像には、あらゆる範囲の3Dスキャンを統合することができます。「デジタルツインのすべての計画データを統合することで、将来の生産計画の全体像を、何年も前に見ることが可能になりました」。それには、実際の工場と同様に、新しいアウディモデルに加え、製造現場、コンベアテクノロジー、ツール、棚、コンテナも含まれています。
組み立てシーケンスとロジスティクスの側面は、主に3Dプロセスワークショップと呼ばれるクロスファンクションチームによって設計および最適化されています。アウディは、デジタルツインと社内VRソリューションにより、デジタル化と視覚化のメリットを活用しています。これらには、毎日更新されるコンポーネントデータと、様々なクルマのバリエーションのビューが含まれます。「何よりも、私たちは生産開始後の全体像を見ています」とアンドレス コーラーは説明しています。その上で彼は、依然として協力関係が重要な要素であると強調しています。「VRメガネを装着し、仮想世界でアバターとして同僚と会う瞬間、私はいつも感動しています。まず、そこで新しいアウディを構築するにあたり、コンピューターで生成されたアバターを見て、それがリアルタイムのシミュレーションにどのように適用されるかを確認します。そして、必要に応じて、必要なツールの材料を設定する方法など、シーケンスや職場環境について一緒に話し合い、最適化します」
アウディはどのようにして生産エネルギーを節減していますか?
インゴルシュタットの拠点が1年間に消費するエネルギーは、市全体が使用する量に相当します。データとデータ分析は、エネルギーを節約するために不可欠なツールです。アウディが社内で開発したエネルギー分析ツールは、リソースを節約しながら製造を持続可能なものにするために役立ちます。これにより、生産時および非生産時に、どこで高いエネルギー消費量が発生しているのかを把握できます。まず、専門家は一貫したデータ形式で様々なソースからデータを収集します。例えば、完成した車両やコンポーネントからのデータ、塗装スプレーブースや溶接ガンからのエネルギーデータ、建物の照明や換気の消費電力に関する情報を収集します。次のステップでは、収集したエネルギー消費量を、エネルギー担当者が理解しやすい形式で提供します。エネルギー担当者は、このデータを基にエネルギーの使用状況を分析します。エネルギー需要が事前に定義された許容限界を超える場合、彼らは原因を調査し、生産中の消費を削減するための措置を講じ、場合によっては生産エリアのベースロード(基礎負荷)を下げます。2021年、アウディはエネルギー分析とプロセスの改善により、インゴルシュタットの拠点で約37,000MWhを節電することに成功しました。
アウディは、生産において、人工知能をどのようにして、どこで使用していますか?
人工知能と機械学習は、アウディのデジタル化への変革プロセスと最先端の生産における主要なテクノロジーです。インゴルシュタットのプレス工程に導入されているAIアルゴリズムは、コンポーネントの欠陥を特定するのに役立ちます。その手順は、人工ニューラルネットワークに基づくソフトウェアによってサポートされています。このソフトウェアは、たとえ微小な欠陥でも識別し、それらを確実にマーキングします。このソリューションは、ディープラーニング、つまり構造化されていない高次元のデータ量を処理できる特殊な機械学習に基づいています。チームは数百万のテストパターンを使用して、数か月にわたって人工ニューラルネットワークの学習を行いました。そのデータベースは、アウディおよびフォルクスワーゲンの数カ所の拠点のプレス工程から得られた、数テラバイトの画像から構成されています。
別のパイロットプロジェクトでは、人工知能を使用して、ネッカーズルム拠点で生産におけるスポット溶接の品質をチェックしています。Audi A6のボディコンポーネントを組み立てるには、約5,300のスポット溶接が必要です。これまで、製造スタッフはランダム化された超音波分析を使用して、抵抗スポット溶接(ドイツ語略語WPS)の品質を監視してきました。WPS分析パイロットプロジェクトの一環として、専門家は人工知能(AI)を使用して、品質の異常をリアルタイムで自動的に検出します。現在、アルゴリズム、ダッシュボード、詳細品質分析アプリケーションはすべて、Audi A6およびA7のボディを組み立てるために使用されています。これは、ネットワーク化された生産における他の用途に活用することができます。
Edge Cloud 4 Production コンセプトの背景とは?
ローカルサーバーソリューションのEdge Cloud 4 Productionにより、アウディはファクトリーオートメーションのパラダイムシフトを始めています。Audi Production Lab(P-Lab)でのテストが成功した後、3台のローカルサーバーがベーリンガーホフ工場の作業者のサポートを引き継いでいます。ネッカーズルムにおける生産では、Audi e-tron GT quattroとAudi R8が組立ラインを共有しています。これらの小規模生産車は、P-Labプロジェクトをテストしたり、大規模な生産で試してみるのに適しています。アウディは、サイクルに依存する生産において、この種の集中型サーバーソリューションに目を向けた世界初のメーカーになりたいと考えています。今後もサーバーインフラがの信頼性が高まれば、アウディはこの世界で唯一の自動化テクノロジーを、グループ全体の量産工程に展開したいと考えています。
Edge Cloud 4 Productionを使用すると、いくつかの集中型およびローカルサーバーが、無数の高価な産業用PCの作業を引き受けることができます。このサーバーソリューションにより、仮想化されたクライアントの総数を一定に保つことが可能になり、リソースをはるかに効率的に使用できます。特にソフトウェアを導入する場合、オペレーティングシステムを変更する場合、IT関連のコストが発生する場合に、効率的な生産を行うことができます。AUDI AG生産およびロジスティクス担当取締役 ガード ウォーカーは次のように述べています。「私たちがここで行っていることは、まさに革命です。これまで、新しい機能を導入したいときは、ハードウェアを購入する必要がありました。Edge Cloud 4 Productionでは、ソフトウェアのアプリケーションのみを購入します。これは、ITベースの生産に向けた重要なステップです」
将来のデジタル化された生産のための新しいアイデアはどこから生まれますか?
アウディは、ミュンヘン工科大学およびフラウンホーファー産業工学組織研究所(IAO)と緊密に協力して、ドイツのハイルブロンの教育キャンパスでデジタル化の実現に取り組んでいます。アウディのAutomotive Initiative 2025(AI25)は、デジタルファクトリーの変革と革新に関して、世界をリードする専門知識のネットワークを確立することを目的としています。AI25は、それ自体がアイデアの発信元であり、デジタルへの移行の重要なコンポーネントと見なされています。アウディのネッカーズルム拠点は、フォルクスワーゲングループのデジタル化への変革におけるパイロットファクトリーとして極めて重要な役割を果たしています。その中で、ベーリンガーホフ工場の実際の実験室から貴重なデータが得られています。さらに、アウディはガイマースハイムにある生産ラボを使用して、新しく革新的なテクノロジーを特定し、それらを生産順序に確実に統合しています。専門家は、ユーザーとの緊密な対話を通して、量産に対する新しいソリューションの適用性をテストしています。
TechDay Smart Production プレスキットは、Audi MediaCenterから入手可能です。
※本リリースは、AUDI AG配信資料の翻訳版です。